What is Just-In-Time Manufacturing?
Just-In-Time (JIT) manufacturing is a strategy that synchronizes production and delivery with real demand. Instead of producing goods in advance and storing them in warehouses, exporters and importers only make and ship products as they are needed. This method helps lower costs and improve efficiency throughout the entire supply chain.
Storing large amounts of inventory can be expensive. For importers, costs add up at every stage—manufacturing, shipping, and warehousing—before a single sale is made. For instance, producing a batch of goods might take 30 days, shipping could add another 30 to 60 days, and then selling the product might take even longer. Each delay increases costs.
JIT addresses these challenges by focusing on producing and delivering goods only when there is a confirmed need. As a result, storage costs go down, products sell faster, and companies have better cash flow. This approach keeps businesses more competitive and lets them quickly respond to what their customers want.
The 5 Principles of JIT Manufacturing
JIT manufacturing follows the Five Zeros to reduce waste and keep operations efficient. These principles guide businesses to produce only what is needed and avoid delays or extra work.
- Zero Inventory: Make products only when there is demand. Keep stock levels low to avoid storage costs.
- Zero Defects: Aim for high quality at every step. Fix problems early to prevent waste.
- Zero Delays: Ensure production moves smoothly. Avoid waiting times and bottlenecks.
- Zero Waste: Eliminate extra steps and unnecessary materials. Focus on lean processes.
- Zero Paperwork: Use digital tools to reduce manual work. Simplify tracking and communication.
What are the Advantages of Just-In-Time Manufacturing?
- Improved Manufacturing Efficiency: Simplifies production processes to reduce waste and boost efficiency.
- Streamlined Supply Chains: Promotes better communication and coordination between suppliers, manufacturers, and customers.
- Lower Inventory Costs: Minimizes expenses tied to storing, managing, and holding large stock levels.
- Space Savings: Frees up warehouse space, reducing the need for large storage areas.
- Higher Product Quality: Encourages ongoing quality checks and quick problem-solving to improve standards.
- Increased Flexibility: Makes it easier to adjust production based on changing customer demands.
- Reduced Waste: Eliminates overproduction, defects, and unnecessary steps, creating a more sustainable process.
- Better Cash Flow: Frees up funds by lowering the amount of money tied up in inventory.
- Customization Options: Enables faster turnaround times for tailored products or special requests.
- Competitive Edge: Responds quickly to market changes, keeping businesses ahead of competitors.
How Does Just-In-Time Manufacturing Work?
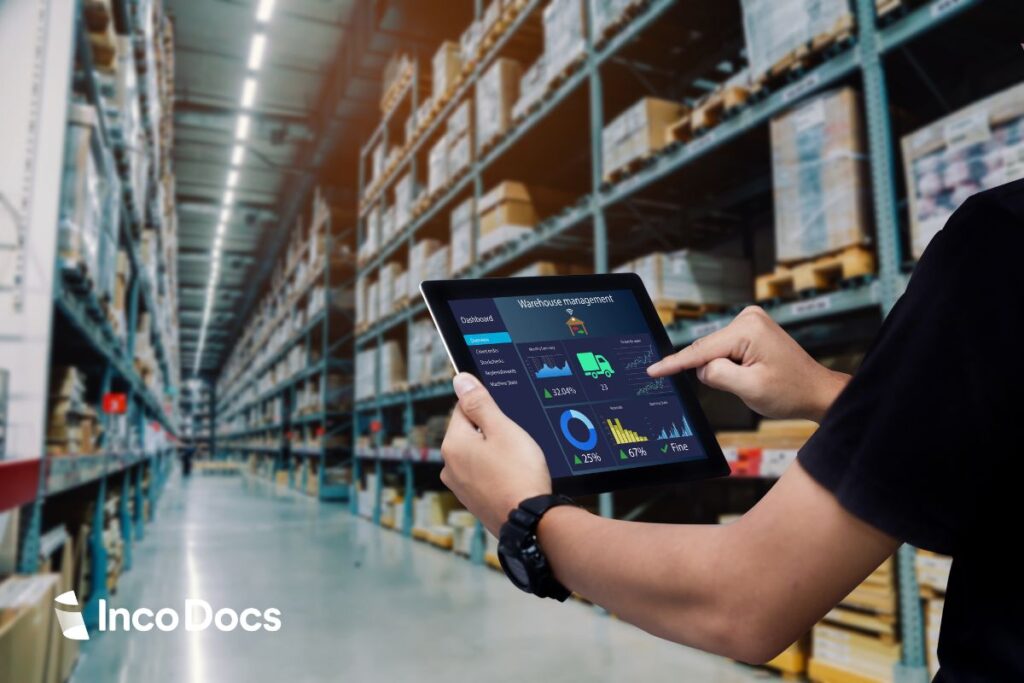
Just-In-Time manufacturing works by closely aligning production schedules with customer demand, Imagine a laptop assembly company. Instead of keeping large stocks of parts like screens and batteries, the company only orders these parts after a customer places an order.
As soon as the order is confirmed, the supplier is informed and delivers just the right amount of parts needed. Once the parts arrive, the assembly team immediately starts building the laptop. After the laptop is finished, it goes straight to the customer, eliminating the need for storage at any stage.
This system runs smoothly because each step is carefully planned. Materials arrive exactly when they’re needed, production starts as soon as those materials are in hand, and the final product is shipped right away without delays.
In summary:
- Direct Delivery to Customers: Finished products are shipped immediately after they’re completed.
- Materials Arrive When Needed: Suppliers deliver parts just in time for assembly.
- Production Begins Quickly: The assembly line starts work as soon as parts arrive.
What are the Disadvantages of Just-In-Time Manufacturing?
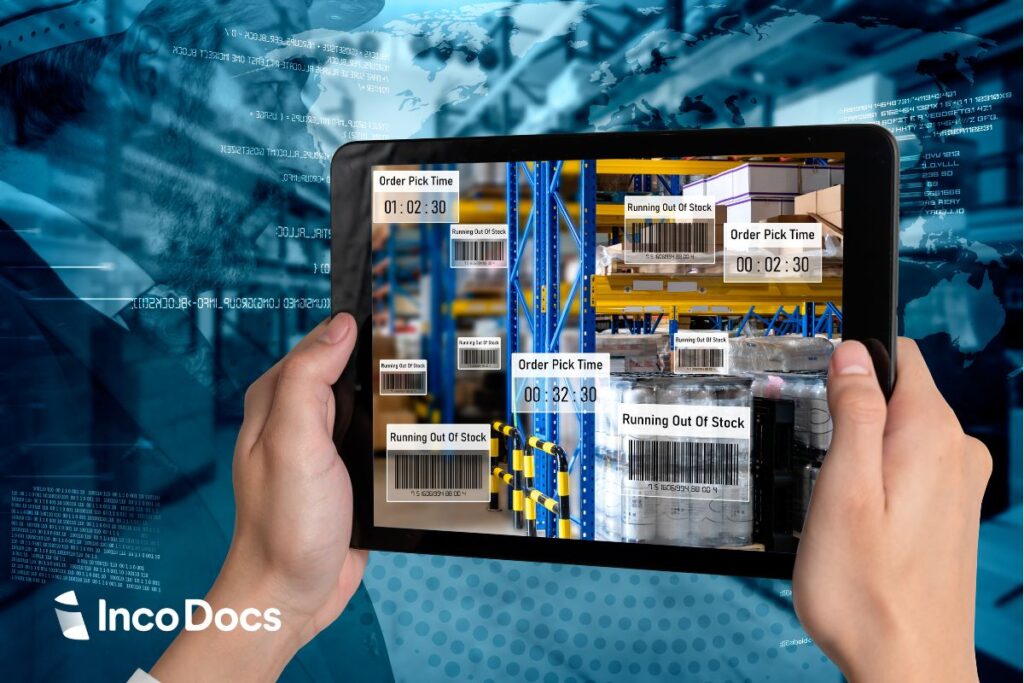
- Supply Chain Disruptions: Delays caused by natural disasters, shipping issues, or supplier failures can stop production.
- Supplier Dependence: Businesses rely heavily on suppliers to deliver materials on time.
- Demand Uncertainty: Mistakes in forecasting can lead to shortages or overproduction.
- Higher Coordination Needs: JIT requires precise scheduling and planning across all areas.
- Risk of Stockouts: Low inventory levels mean companies have less room to handle sudden demand increases.
- Investment in Systems: Advanced tools are often needed for tracking, forecasting, and managing inventory.
- Quality Control Pressures: Faster production cycles can make it harder to maintain consistent quality.
Why Has Just-In-Time Manufacturing as a Strategy Increased Over the Past Few Years?
In recent years, more businesses have switched to JIT manufacturing due to issues like trade disputes and shipping delays. These problems make it challenging to hold large amounts of inventory. By using JIT, companies rely on smaller, more frequent deliveries, allowing them to keep less stock on hand and adapt quickly when circumstances change.
Advances in technology have also made JIT easier to implement. Modern data systems and tracking tools help companies plan more effectively, work smoothly with suppliers, and monitor materials throughout the process.
What Types of Companies use Just-In-Time Manufacturing?
Many industries have adopted JIT manufacturing to stay efficient and reduce costs. One of the most famous examples is Toyota. In the 1970s, Toyota built its production system around JIT principles. These ideas, introduced by Taiichi Ohno, helped the company reduce waste and improve processes. Today, the Toyota Production System is seen as a global standard for lean manufacturing.
Tech companies like Dell also rely on JIT. They assemble computers only after receiving orders. This avoids storing extra parts and keeps products up to date. The system lowers storage costs and prevents outdated inventory.
In fashion, brands like Zara use JIT to match seasonal trends. They produce clothing as needed, avoiding overproduction. This ensures stores stay stocked with the latest designs. Even fast-food chains like McDonald’s prepare food only when ordered. This reduces waste and keeps meals fresh.
More examples below,
- Toyota (Japan): Pioneered the JIT concept as part of the Toyota Production System, becoming a global benchmark for efficiency and lean manufacturing.
- Dell (United States): Utilizes JIT to manage inventory and production, customizing computers based on customer orders and minimizing warehouse storage.
- Harley-Davidson (United States): Implemented JIT to streamline operations, reduce costs, and improve flexibility in manufacturing processes.
- Nissan (Japan): Applies JIT principles to optimize inventory management and production efficiency, enhancing its global competitiveness.
- Apple (United States): Employs JIT in its supply chain to manage the production of its devices, ensuring timely delivery of components and products.
- McDonald’s (United States): Uses a form of JIT in its kitchens, preparing food as orders are placed to ensure freshness and reduce waste.
- Zara (Spain): Operates a JIT system in its supply chain to quickly move designs from concept to store shelves, keeping inventory levels low and responding swiftly to fashion trends.
- Samsung Electronics (South Korea): Implements JIT to manage component supplies for its electronics manufacturing, reducing lead times and inventory costs.
- IKEA (Sweden): Adopts JIT principles in its supply chain to minimize storage needs and efficiently manage inventory of its flat-packed furniture.
- Boeing (United States): Applies JIT methodologies in the production of aircraft, coordinating the delivery of parts to align with assembly schedules to reduce inventory storage.
- Intel (United States): Uses JIT to streamline its semiconductor manufacturing processes, ensuring timely delivery of materials and reducing inventory levels.
Video Insight: JIT Inventory Management in Action By Toyota
What is Just-In-Case Manufacturing?
Just-In-Case (JIC) manufacturing is the opposite of Just-In-Time (JIT). Instead of minimizing inventory, it focuses on keeping extra stock. This helps businesses deal with unexpected issues like supply delays or sudden demand spikes.
Some industries need this backup approach. Medical supplies, hospitals, and the military rely on JIC to ensure critical items are always available. These sectors cannot afford to run out of stock, even if deliveries are late or disrupted.