Causes For Shipping Delays In 2025
In 2025 the world of international shipping is still facing big logistical challenges that slow down global trade. These include ongoing regional conflicts like the situation in the Red Sea and the war in Ukraine. Tensions between the US and China have also added new uncertainty for global supply chains. On top of that the drought in Panama is still causing major delays at the canal which remains one of the most important shipping routes in the world.
This article breaks down 20 reasons your shipments might be delayed and what you can do to work around them. It’s more important than ever for businesses to stay on top of these issues so they can manage delivery times and keep customers happy.
U.S.–China Trade Tensions and Cancelled Sailings
In 2025, trade tensions between the U.S. and China are once again causing major shifts in global shipping. New tariffs and the end of the de minimis rule for shipments under $800 from China have made it harder and more expensive to import goods. This change has led to fewer orders being placed, especially by big retailers.
With demand dropping, many shipping lines are cancelling sailings between Asia and North America. These blank sailings are now making it tough for businesses to find space on vessels. The result? Longer delays, higher costs, and more pressure on supply chains that rely on fast and frequent deliveries.
Pirates
Pirates are a real threat to shipping, especially in certain parts of the world. Ships passing through high-risk waters, like the pirates at the Red Sea and the Gulf of Guinea, are vulnerable. Pirates can capture ships to demand ransoms, causing significant delays and raising security concerns.
Shipping companies often hire armed guards to protect their vessels in these dangerous areas. Despite this protection, the threat of piracy can still cause route changes. Such detours lead to longer delivery times and higher shipping costs.
Moreover, the impact of piracy extends beyond immediate threats. It can lead to increased insurance costs for shipping companies. These costs may be passed on to consumers in the form of higher prices for goods. Hence, piracy affects the economy and shipping efficiency globally.
War and Conflicts
War and conflicts can severely disrupt shipping routes and delay deliveries. In areas of armed conflict, ports may close, and maritime channels can be blocked. This forces ships to take longer, alternate routes, increasing travel time and costs.
For example, during the Russian-Ukraine conflict, the region’s shipping operations faced significant disruptions. Similar situations have occurred when tensions escalated in other parts of the world, affecting global trade routes. Companies often must reroute their shipments to avoid conflict zones, which leads to delays.
Moreover, war and conflicts can result in stricter security measures at ports and increased inspections. This can further slow down the process of shipping goods, as every cargo batch undergoes thorough checks. These factors together make trading in and through conflict-affected areas both challenging and expensive.
Global Emergencies
Global emergencies, such as pandemics and natural disasters, dramatically affect shipping timelines. For example, during the COVID-19 pandemic, shipping industries faced severe delays due to lockdowns and restrictions. Ports operated at lower capacities, which slowed down the loading and unloading of goods.
Natural disasters like hurricanes or earthquakes can damage ports and disrupt sea routes. This damage often takes time to repair, leading to significant delays. For instance, a hurricane might close a major port for days or even weeks, forcing ships to wait or reroute.
Delayed shipments caused by global emergencies can lead to sudden changes in market demands. During the pandemic, there was a shift from buying services to buying goods, overwhelming shipping services. Such shifts can strain logistics networks, extending delivery times and affecting supply chains worldwide.
Weather Anomalies
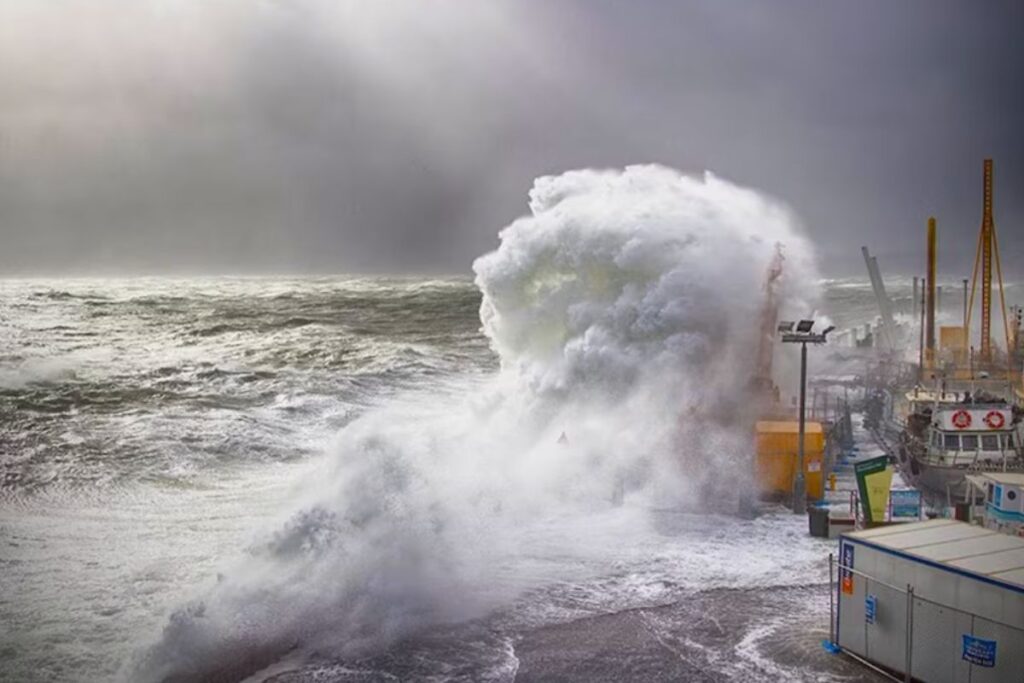
Weather anomalies, like storms and hurricanes, have a big impact on shipping carriers. Bad weather can delay container ships by forcing them to take longer routes or stop at safe ports until it’s safe to continue.
Heavy rains and floods can also damage roads and railways. This makes it hard for trucks and trains to deliver goods from ports to stores and warehouses. When transportation routes are blocked or damaged, it causes more delays and problems down the supply chain.
The opposite can be equally disrupting. The drought affecting the Panama Canal has led to substantial disruptions. Reduced water levels mean fewer vessels can navigate the canal each day, and ships must carry less than their maximum capacity. This situation has significantly increased shipping costs.
To minimize the effects of bad weather, shipping companies track weather closely. They plan routes that avoid major storms and adjust schedules in advance. This planning helps reduce delays, but sometimes, the weather is too unpredictable and still causes problems.
National and International Holidays
National and international holidays can lead to significant shipping delays. During these times, customs offices and shipping companies often reduce their operations or close completely. This break can slow the processing of goods through ports and delay their delivery.
Holidays also coincide with high shopping periods, like Christmas or Chinese New Year, when there is a surge in demand for goods. This increase in volume puts extra pressure on shipping services and can cause further delays. Ports become busier, and it takes longer to handle the large numbers of shipments.
To cope with holiday-related delays, companies should plan ahead. They can schedule shipments earlier or use different routes to avoid busy ports. By preparing for these predictable disruptions, businesses can better manage shipping times and keep their customers satisfied.
Incorrect Shipping Data
Incorrect shipping data, such as wrong addresses, incorrect phone numbers, or errors in documentation, can cause significant delays in the delivery process. These mistakes can send packages to incorrect destinations or cause issues at customs where precise information is crucial for clearance. Common documents where errors frequently occur include bills of lading, commercial invoices, and customs declarations.
When couriers have inaccurate information, they waste time trying to locate correct delivery points. This not only delays the specific shipment but can disrupt the overall delivery schedule, impacting many shipments in the system. Misinformation can also cause shipments to be held at customs, significantly extending the waiting period for clearance.
To minimize these delays, businesses must ensure all shipping data and documents are double-checked before goods are dispatched. Implementing automated systems that verify addresses and documentation details can help reduce errors. Keeping shipping data accurate is essential for efficient delivery and customer satisfaction, helping to streamline the entire shipping process.
Customs Hold-Ups
Customs hold-ups are a common reason for shipment delays at the border. These delays happen when shipments do not meet the specific regulations of the importing country. Issues often involve missing or incorrect documents such as customs declarations, import licenses, and certificates of origin. Without the right paperwork, customs authorities cannot process and clear the shipments, leading to hold-ups.
To reduce the risk of customs hold-ups, businesses should ensure all required documents are accurate and complete before shipping. It’s also beneficial to stay updated on the customs regulations of the destination country to avoid non-compliance with new or updated laws. Proper preparation and knowledge can help smooth the passage of goods through customs and prevent unexpected delays.
Traffic Challenges and Schedule Changes
Traffic challenges significantly impact delivery times, particularly in urban areas. Road congestion can slow down the delivery trucks, making it hard to maintain schedules. This type of delay affects the timely arrival of goods to warehouses and stores, disrupting planned stock levels and potentially leading to shortages.
Schedule changes often occur as a direct response to traffic challenges. Shipping companies may adjust delivery routes or schedules to avoid peak traffic times or congested routes. However, these changes can complicate logistics, requiring more coordination and sometimes leading to longer transit times.
To manage these issues, companies use advanced route planning software to find the most efficient paths. They also schedule deliveries during off-peak hours to avoid the busiest times. These strategies help minimize the impact of traffic challenges and keep deliveries running smoothly.
Port Congestions and Strikes
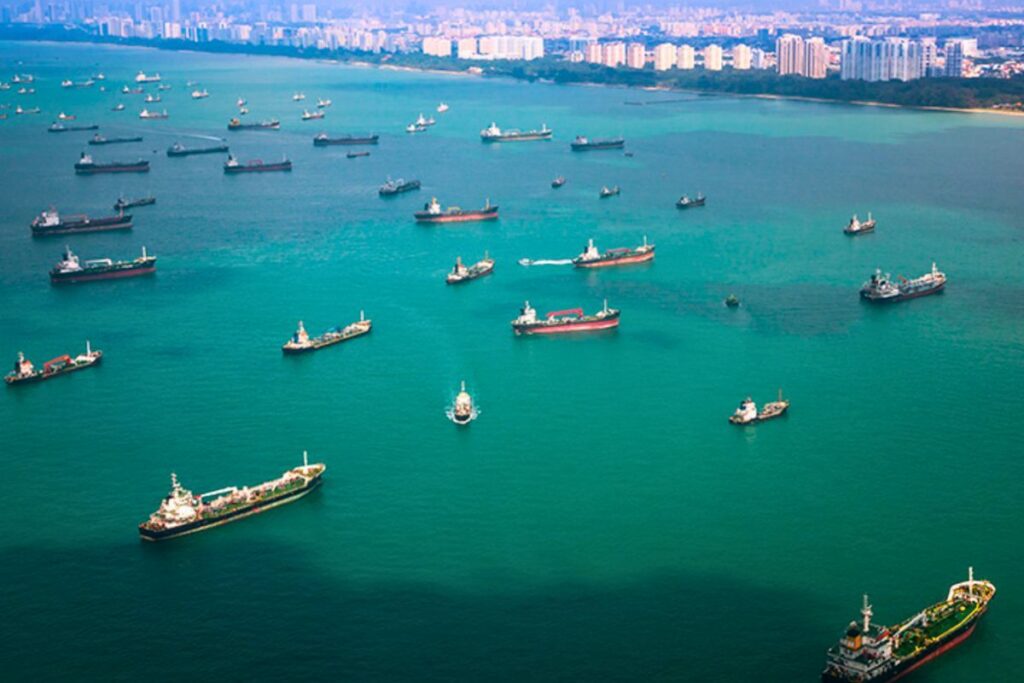
Port congestions and strikes are major causes of shipping delays. When ports are too crowded, ships must wait their turn to dock and unload goods. This waiting leads to delays in the supply chain, affecting everything from production schedules to product availability. Congestion often occurs during peak shipping seasons or when ports lack sufficient capacity to handle the volume of traffic.
Strikes by port workers complicate the situation further. If workers are striking, unloading containers and processing of cargo slow down or stop entirely. This can cause significant delays because no goods are moving in or out of the port. Strikes may arise from disputes over wages, working conditions, or changes in employment terms. A strike at the US West Coast would cost the economy 500 Million dollar a day.
Recently in March 2025, multiple strikes occurred in French ports, including a 72-hour total shutdown. These labor actions caused significant congestion and delays in cargo handling, affecting shipping schedules across Europe.
To reduce the impact of port congestions and strikes, companies often use alternate ports or adjust shipping schedules ahead of time. They may also stockpile goods to cushion the effects of expected delays. These strategies help businesses maintain smoother operations despite disruptions at ports.
Delayed Cargo Production
Delayed cargo production can have a significant impact on shipping schedules. When manufacturing slows down, it delays the production of goods. This in turn affects the timing of when products are ready to be shipped. If goods are not ready on time, it can lead to missed shipping slots, further delaying their arrival to the market.
Slow manufacturing can be caused by various factors such as shortages of raw materials, equipment malfunctions, or labor issues. These delays can ripple through the supply chain, affecting everything from warehouse operations to final delivery to customers. It can also cause congestion in storage areas as goods pile up waiting to be shipped.
One strategy to manage such impacts is just-in-time (JIT) production, which aligns manufacturing processes with order demands, reducing the need for large inventories. However, while JIT can enhance efficiency, it also requires precise coordination. Any delay in production can disrupt the entire supply chain, emphasizing the need for reliable manufacturing processes to keep shipments on schedule.
Rolled Shipments
Rolled shipments, also known as rolled cargo, occur when cargo ships are overbooked, and there isn’t enough space for all the booked cargo. This often happens during peak shipping seasons when demand for cargo space exceeds the supply. When shipments are rolled, they are not loaded onto the ship as planned and must wait for the next available shipping opportunity.
This delay can disrupt supply chains and schedules. Businesses relying on timely deliveries to meet customer demands can face challenges, such as stock shortages or delayed product launches. These issues can lead to dissatisfied customers and potential financial losses for companies.
To avoid the problem of rolled shipments, companies can book space well in advance or use alternative shipping routes and carriers. They may also consider spreading their shipments across different ships to reduce the risk of having a large amount of cargo rolled at once. These strategies help ensure smoother operations and reduce the likelihood of significant disruptions caused by overbooked cargo ships.
Damaged Cargo
Damaged cargo often leads to delays in the shipping process. When goods are damaged during transportation, they need to be inspected, repaired, or sometimes replaced entirely. This can halt the delivery process as necessary actions are taken to resolve these issues. Such damage can occur due to improper packing, rough handling, or accidents during transit.
Handling damaged goods requires additional time and resources. Companies must assess the extent of the damage, communicate with customers, and determine the best course of action, whether that’s sending replacement products or offering refunds. This not only delays the shipment but can also affect customer satisfaction and trust.
To minimize the occurrence of damaged cargo, it’s crucial for businesses to invest in quality packaging and handle goods with care throughout the shipping process. Using reliable shipping services that have robust handling procedures also helps reduce the risk of damage. These measures can significantly decrease the likelihood of delays related to transportation mishaps.
Technical and Mechanical Issues
Technical malfunctions in transportation equipment can lead to significant delays in deliveries. If a ship, truck, or plane experiences a mechanical issue, it may need to be repaired before continuing its journey. This can cause the goods being transported to arrive later than expected. Equipment failures are especially problematic because they are often unexpected and can occur anywhere along the transport route.
For instance, if a ship’s engine breaks down, it may be stuck at sea or need to dock for lengthy repairs. Similarly, if a delivery truck breaks down, the goods must wait until the truck is fixed or a replacement vehicle is sent. These delays disrupt the entire delivery schedule, affecting not only the current cargo but also future shipments scheduled to use the same vehicle.
To mitigate the impact of technical malfunctions, companies invest in regular maintenance of their transportation equipment. This preventative measure helps identify potential issues before they lead to breakdowns. Additionally, having backup plans such as spare vehicles or alternate shipping methods can help keep deliveries on track despite unexpected equipment failures.
Ineffective Transportation Planning
Ineffective transportation planning often leads to frequent delays in shipping. When logistics are not carefully managed, vehicles may not be loaded efficiently, routes might not be optimized, and schedules can be unrealistic. These planning failures cause delays because each part of the transport chain affects the next, creating a domino effect that disrupts the entire delivery timeline.
Poor route planning is a common issue. If routes are not optimized for traffic patterns, road conditions, and delivery locations, drivers can spend more time on the road than necessary. This not only slows down deliveries but also increases fuel consumption and wear and tear on vehicles. Moreover, failing to account for potential disruptions like road construction or heavy traffic can further delay transportation.
To improve transportation planning, companies use advanced software to optimize routes and schedules. This technology considers various factors, including traffic, weather, and vehicle capacity, to ensure more efficient and reliable delivery schedules. Regular training for logistics staff also helps in adopting best practices and enhancing the overall planning process. These efforts streamline operations and reduce the likelihood of delays.
Shipping Documentation Errors
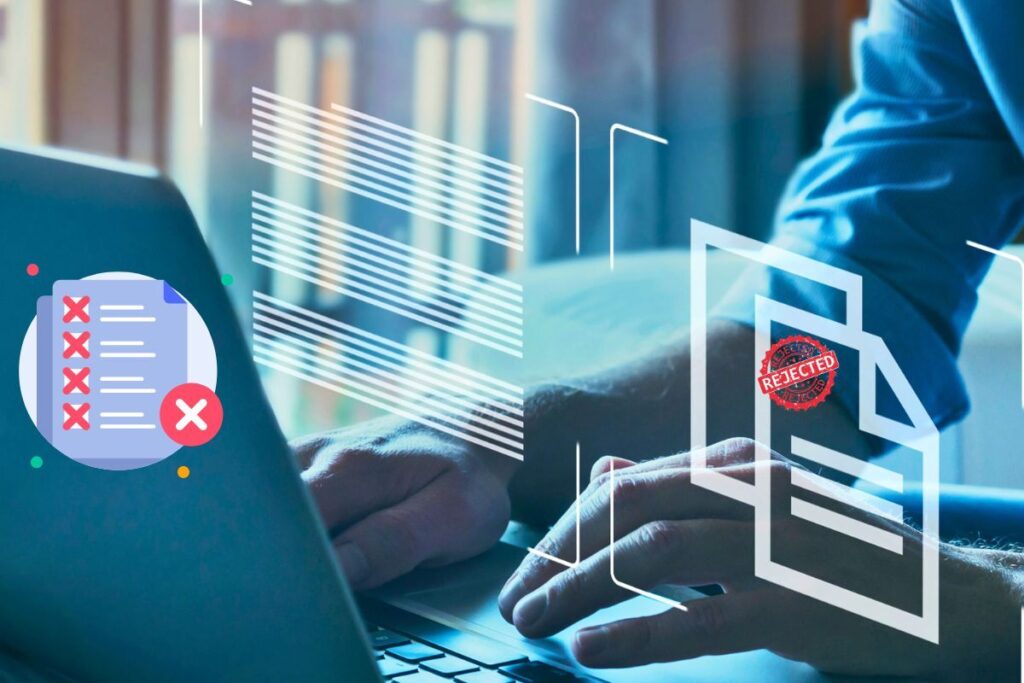
Shipping documentation errors are a major cause of hold-ups in the delivery process. Incorrect or incomplete paperwork can prevent cargo from being loaded onto ships or cleared through customs. This includes errors in commercial invoices, packing lists, and bills of lading. When these documents don’t match the actual cargo or lack necessary information, authorities may delay the shipment until issues are resolved.
One common documentation error involves discrepancies in the listed quantities or descriptions of goods. Such mistakes can lead to suspicions of smuggling or fraud, prompting thorough inspections. These inspections not only delay the specific shipment but can also backlog other deliveries scheduled for the same route or vehicle.
To prevent paperwork problems, companies need to ensure that all shipping documents are double-checked for accuracy before submission. Employing trained specialists or using automated software solutions can help streamline this process and reduce human error. These measures improve the accuracy of documents and help maintain smooth shipping operations.
Lack of Visibility in Shipping Processes
Lack of visibility in shipping processes often leads to hidden delays. Without clear tracking and updates, it’s hard to know where goods are at any moment. This uncertainty can cause delays as businesses cannot react quickly to issues that may arise during transit. Without visibility, unexpected problems like misroutes or hold-ups at customs can go unnoticed until they cause significant setbacks.
For instance, if a shipment is stuck at a port due to documentation issues but the company is unaware, they cannot address the problem promptly. This lack of real-time information can extend the delay, affecting the delivery schedules and potentially the supply chain. Such scenarios are common when businesses do not have systems in place to monitor the movement of their goods.
Improving visibility in shipping involves investing in technology such as GPS tracking and real-time data systems. These tools allow companies to monitor their shipments closely and manage them proactively. By having access to up-to-date information, businesses can better predict arrival times, plan for potential delays, and communicate effectively with customers and partners about the status of their goods.
Hours of Service (HOS) Restrictions
Hours of Service (HOS) restrictions significantly impact shipping timelines. These regulations limit the number of hours truck drivers can operate in a day and week to ensure safety. When drivers reach their hour limits, they must stop and rest, delaying the transport of goods. This is essential for preventing fatigue-related accidents but can slow down delivery schedules.
For example, if a driver has only a few hours left on their HOS clock but a delivery is several hours away, they must stop and rest before completing the trip. This can lead to late deliveries, especially if no other drivers are available to take over. Companies must plan meticulously around these regulations to maintain timely deliveries.
To manage the impact of HOS restrictions, companies use route planning software to maximize efficiency within the allowed driving hours. They may also employ more drivers to ensure that when one must rest, another can continue with the deliveries. This strategy helps mitigate delays while complying with safety regulations, ensuring that goods arrive on time without overworking drivers.
Lost Freight
Lost freight is a significant challenge in the shipping industry, leading to delays and financial losses. When shipments are misplaced, they do not reach their intended destination on time, if at all. This can happen due to labeling errors, handling mistakes, or incorrect loading at ports. The confusion from lost freight affects not only the immediate delivery but also disrupts inventory levels and planning.
Finding lost shipments requires time and resources. Companies often need to trace back through the shipping process to discover where the error occurred. This detective work is costly and time-consuming. Meanwhile, customers are waiting, which can lead to dissatisfaction and damage to the company’s reputation.
To minimize the risk of lost freight, companies invest in better tracking systems that monitor shipments from origin to destination. Barcode scanning and GPS tracking are tools that help keep tabs on cargo, providing updates at every stage of the journey. These technologies help quickly identify when and where a shipment goes off course, allowing for faster resolution of issues.
Customs Inspections
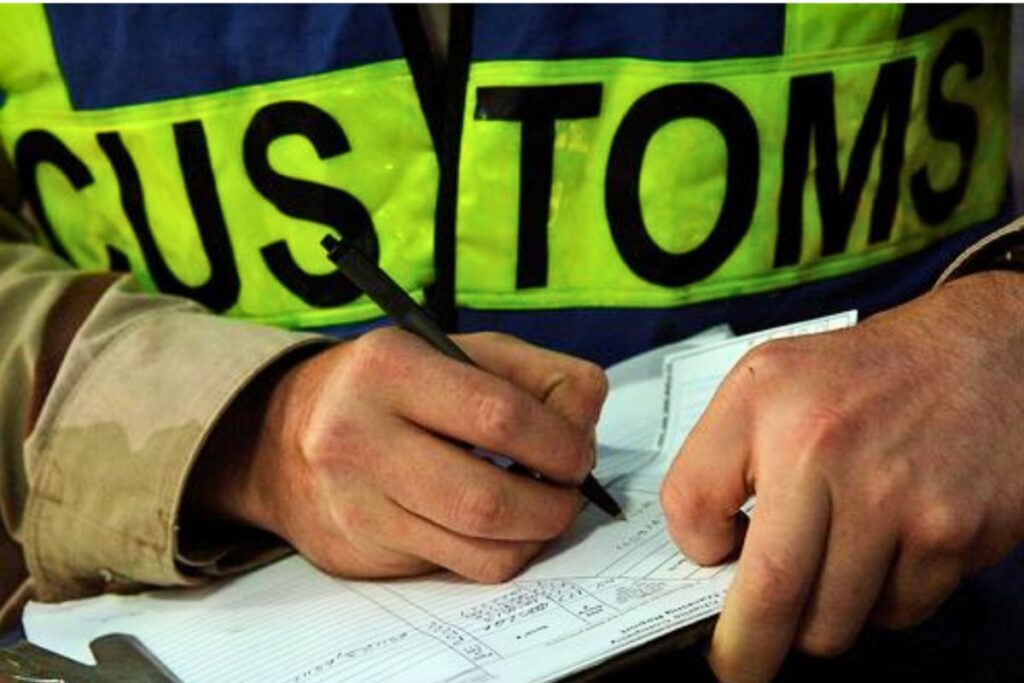
Customs inspections are necessary for verifying that goods entering a country meet all regulations and laws. These checks ensure that no prohibited or undeclared items cross borders. It can be a common cause for a delay when the shipment requires thorough inspection. This thorough examination can take time, especially if the paperwork is not in order or if the shipment is large.
During these inspections, customs may require additional documentation or even physical checks of the cargo. If discrepancies are found, such as mismatched documentation or mislabeled goods, resolving these issues can extend the delay. In some cases, entire shipments may be held until the necessary corrections are made, affecting the delivery schedule of these goods and potentially others waiting in line.
To reduce the likelihood of delays caused by customs inspections, businesses should ensure that all shipping documents are accurate and complete before dispatch. It is also helpful to stay updated on the customs regulations of the destination country to prevent any compliance issues. Being proactive in these preparations can streamline the customs process and minimize delays.