What is a stowage plan for container ships?
Container stowage planning is the process of organizing and allocating space on a cargo ship for containers. It’s purpose is that containers are planned and loaded efficiently. This maintains balance and safety.
Stowage plans are like blueprints for designing the placement of shipping containers. Without proper stowage plans, ships risk instability, cargo losses, and delays. Effective stowage planning enhances operational efficiency and boosts revenue for shipping companies and ports. Stowage plans are also important for crew and cargo safety.
What is container stowage planning?
Container stowage planning involves two key steps. First, it ensures cargo is loaded efficiently into containers, filling them to capacity. Second, it manages the placement of these containers onto the ship to maximize the number carried in one trip. This optimizes space and prevents economic losses from poor container organization.
For example, LCL (Less than Container Load) shipments combine multiple small shipments into one container. With the help of a CBM calculator, shippers can prevent waste of space in LCL shipments. This method makes shipping more economical. similarly with containers, if they are not properly arranged on the ship, they can take up unnecessary space, leaving no room for others. Effective stowage planning ensures containers are stacked efficiently, using all available space. This reduces costs, speeds up loading and unloading, and improves overall efficiency.
How to create a stowage plan for cargo containers
Creating a stowage plan involves a systematic approach to ensure efficient and safe cargo loading. First, analyze the ship’s design to maximize available space. This includes the ship’s length, width, and hold capacity.
To create a stowage plan you need to:
- Gather detailed data on each container, such as size, type, weight, and special handling requirements. Plan weight distribution by placing heavier containers at the bottom and lighter ones on top. This helps maintain the ship’s stability.
- Consider the type of cargo; hazardous materials need careful handling, and perishable goods should be near refrigeration units. Identify specific stowage locations for each container, considering rows, tiers, positions, bays, and holds.
- Use proper securing and lashing methods to prevent containers from shifting during transit. Prepare all necessary documentation, including bills of lading and customs paperwork. Continuously monitor the stowage process and make adjustments as needed.
Components that you need for a Stowage Plan
We’ve just covered how to create a stowage plan, these are the actual components required to make a stowage plan:
Container Information:
- Number of containers, type, and size (e.g., 20ft, 40ft).
- Weight and payload details.
Cargo Details:
- Description and quantity of each cargo item.
- Hazardous material classification if applicable.
- Special handling requirements if needed.
Stowage Location:
- Precise location within the vessel (row, tier, position).
- Bay and hold numbers.
- Port of loading and port of discharge.
Weight Distribution:
- Proper distribution to maintain ship stability.
- Compliance with the vessel’s weight and load limits.
- Avoidance of exceeding weight limits on individual bays.
Securing and Lashing:
- Methods for securing containers to the vessel.
- Lashing equipment and techniques.
- Compliance with international lashing standards.
Ventilation and Temperature:
- Requirements for ventilating cargo.
- Temperature control for temperature-sensitive items.
- Monitoring systems for such cargo.
Documentation:
- Bill of lading and other necessary shipping documents.
- Customs and regulatory documentation.
- Instructions for the crew.
- Emergency response plans if required.
Special Requirements:
- Unique requirements or constraints.
- Necessary permits and approvals.
- Compliance with trade sanctions if applicable.
Things to Consider When Making a Stowage Plan
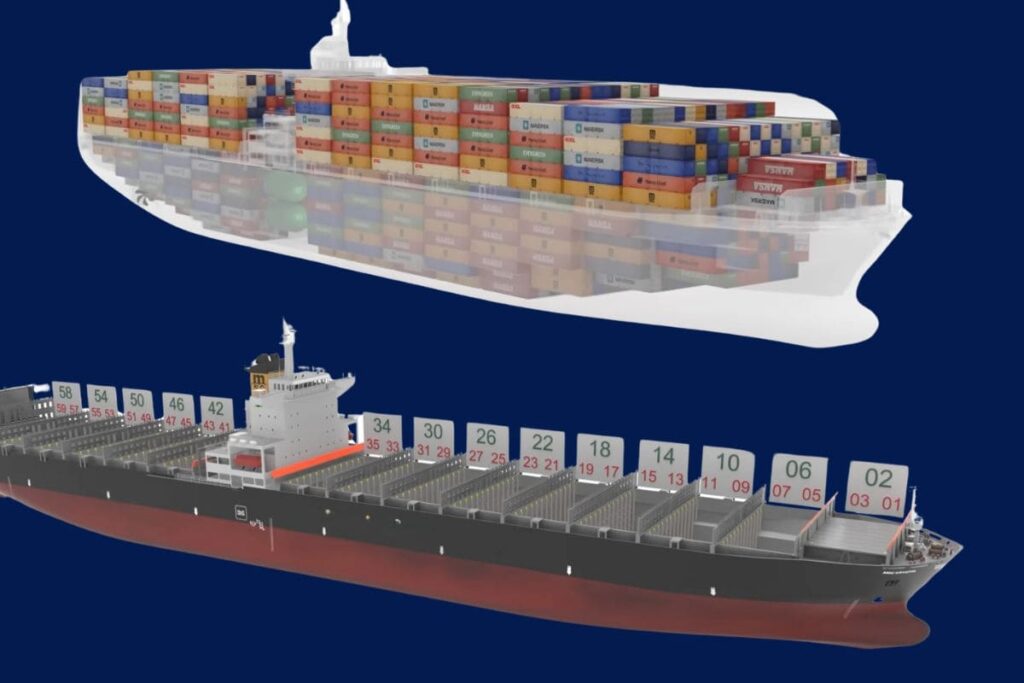
Avoid over-stowage by planning so that cargo for later ports is not placed over cargo for earlier ports. Calculate loading conditions to maintain stability. Ensure that limits for shearing force, bending moment, torsion moment, trim, and draft are not exceeded. Maintain the International Maritime Organization’s (IMO) visibility line on deck.
Stow dangerous goods according to the ship’s Document of Compliance. Manage the Metacentric height (GM) to ensure stability. Typically, light containers are stowed on top of heavy ones. In certain situations, heavy containers may be placed on top with due regard for lashing stresses.
To sum the considerations up::
- Avoid over stowage.
- Calculate loading conditions.
- Handle IMDG containers carefully
- Maintain IMO visibility line: The IMO Visibility Line ensures clear visibility for ship deck officers. It sets limits on how high containers can be stacked on deck. This prevents the bridge view from being obstructed. Maintaining this line is crucial for safe navigation. Stowage planning must consider this to comply with safety regulations.
- Manage GM value: The GM, or Metacentric Height, measures a ship’s stability. It is the distance between the ship’s center of gravity and its metacenter. A higher GM value means better stability and quicker return to an upright position. A low GM value indicates poor stability, making the ship prone to rolling and capsizing. Proper weight distribution in stowage planning ensures a safe GM value.
Different Types of Stowage Plans for Container Ships
There are various types of stowage plans for container ships. Each type depends on how the containers are placed on the ship. Here are the main types:
Cellular Stowage: This is the most common method. Cargo ships designed for cellular stowage have cell guides. Containers are slotted into these vertical cells. This provides extra support and prevents shifting during the voyage.
Bay Stowage: In bay stowage, containers are placed in compartments called bays. These compartments are arranged perpendicular to the ship’s length. This method is ideal for oversized containers, like 53-ft-high cube containers, which need more stability.
Hatch Cover Stowage: Hatch covers are steel structures that cover the cargo hold openings. Some ships place containers on top of these locked hatch covers. This prevents water from entering the hold and allows for more container placement.
Reefer Stowage: Reefer containers are refrigerated and need power sources to stay cool. These containers are placed where repairs, maintenance, and power connections are easy to manage. Efficient reefer stowage ensures that these containers are kept in optimal conditions.
Who makes sure that the stowage plan is followed?
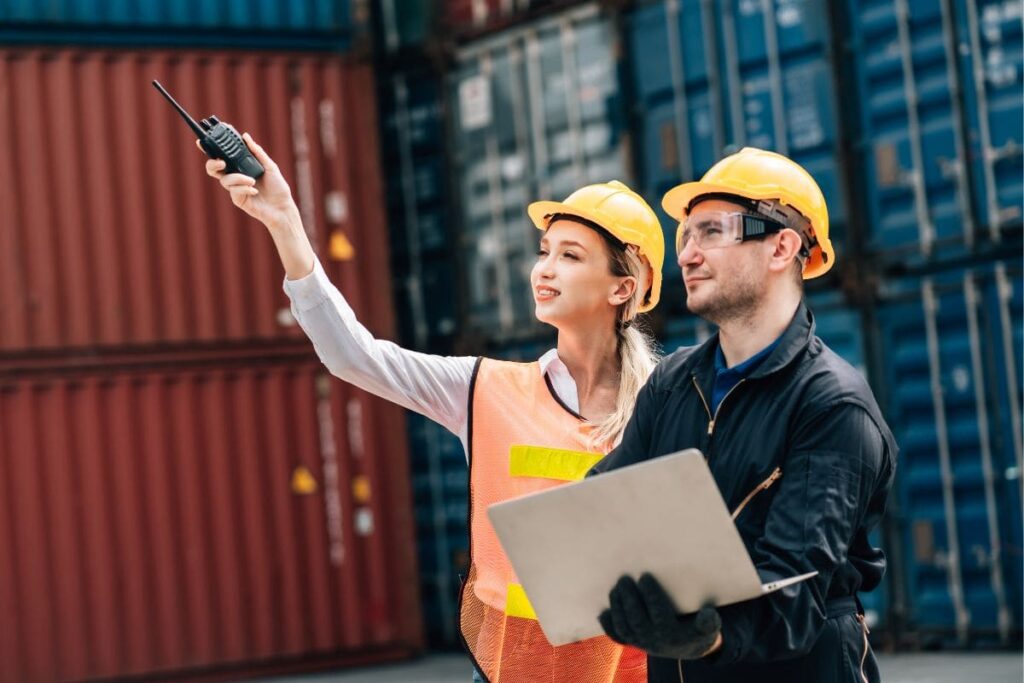
The Chief Officer is primarily responsible for ensuring that the stowage plan is followed on a ship. This officer oversees the loading and unloading processes and verifies that containers are placed according to the plan. The Chief Officer works closely with the ship’s crew, stevedores, and port authorities to ensure compliance. Additionally, the ship’s captain and the shipping company have overall responsibility for the safety and efficiency of the stowage plan.
Benefits of Efficient Stowage Planning
Each stowage type is designed to maximize efficiency and safety for different container needs on a cargo ship. Efficient stowage planning offers many advantages for shipping operations. It improves how space is used on the ship. This leads to lower costs and better safety. Shipping companies and ports both gain from these improvements. Here are some key benefits:
Maximized space utilization is a primary benefit of efficient stowage planning. By carefully organizing containers, every available inch of space on the ship is used. This allows more cargo to be transported in a single trip. As a result, shipping companies can maximize their capacity and efficiency. This reduces the need for additional voyages.
Lower fuel consumption is another significant advantage. When space is maximized, fewer trips are needed to transport the same amount of cargo. This means ships use less fuel overall. Reduced fuel consumption lowers operational costs. It also helps decrease the environmental impact of shipping.
Faster transit times are achieved through efficient stowage. Organized loading and unloading processes save time at ports. Containers are placed in accessible positions based on their destination. This minimizes delays and streamlines operations. Faster transit improves customer satisfaction and service reliability.
Improved cargo safety is a key benefit. Proper stowage prevents containers from shifting during transit. This reduces the risk of damage to the cargo. Securely placed containers also enhance the ship’s stability. This minimizes the chance of accidents at sea.
Economic benefits for shipping companies and ports are substantial. Efficient stowage reduces operational costs by maximizing space and lowering fuel consumption. It also speeds up port operations, increasing throughput. This boosts revenue for both shipping companies and port authorities. Improved efficiency and safety attract more business, further enhancing profitability.