Unloading containers is a crucial step in the shipping process. Shipping containers arrive and need to be carefully unloaded so that the products can be used or onsold into the market.
It may seem like a straightforward process, however many steps should be taken to ensure that the goods are unloaded safely and efficiently without causing any damage or problems.
Efficient unloading not only saves time and cost but also protects workers, goods, and equipment. Below are essential steps and best practices to follow for safe and efficient unloading of shipping containers.
Pre-Arrival Notes and Checks
Efficient and safe unloading begins before the container even arrives at your facility. Preparing in advance helps streamline the process and prevents unexpected delays.
Plan the Container Positioning
Decide in advance where the container will be unloaded and ensure the area is clear and accessible. Consider if the container doors should face a particular direction based on where unloading equipment will be used.
Choose an Unloading Method
Determine whether you’ll need a Live Unload, Drop and Return, On the Chassis or Unloading Dock setup. Select the approach that best fits your facility’s capabilities, your unloading timeline, and the nature of the cargo. Planning for the right method prevents unnecessary delays and keeps operations running smoothly.
Live Unload: A live unload happens when the driver stays on-site while the container is being emptied. This method is common for short stops or when immediate unloading is required. The main advantage is reduced container rental time. The truck and container leave as soon as the goods are unloaded. This method is best for facilities that have adequate staff and equipment ready to unload quickly. However, it can be stressful for teams if delays occur. If the container takes too long to unload, the trucking company will charge additional wait fees. This method requires careful planning and coordination to avoid wasting the driver’s time.
Drop and Return: With the drop and return method, the driver drops the container at the facility and returns later to pick it up. This is ideal for locations that need more time to unload or want to manage unloading during off-peak hours. It provides flexibility and allows workers to unload at their own pace. There’s no pressure to finish quickly, and teams can focus on safe handling. The downside is that it may result in extra charges if the container sits too long. If the unloading is not completed before the agreed pickup time, it can lead to detention fees. This method works best for facilities with flexible schedules and low unloading pressure.
On the Chassis: This approach keeps the container on the truck’s chassis during unloading. It is efficient for light or palletized goods that can be moved quickly. It eliminates the need for additional equipment like cranes to lift the container off the truck. This is often used at sites without docks or when space is limited. However, it’s not suited for heavy items or large loads. Containers on a chassis can be unstable if the cargo is not balanced. This method also ties up the truck during unloading, making it less suitable for busy facilities with high container volumes.
Unloading Docks: Using an unloading dock is the standard method for most large operations. It provides a stable, safe environment for unloading all types of goods. Docks are equipped to handle forklifts, conveyor belts, and other machinery, making it easier to move heavy or bulk items. The main drawback is the need for a dock space. Facilities without docks may struggle to accommodate large volumes or specific container sizes. This method is ideal for facilities that have high unloading volumes and need efficiency.
Prepare Necessary Equipment
Confirm that all necessary equipment such as forklifts, pallet jacks, and container ramps are available and in good working order. Schedule any required safety checks on equipment to avoid unexpected breakdowns during the unloading process.
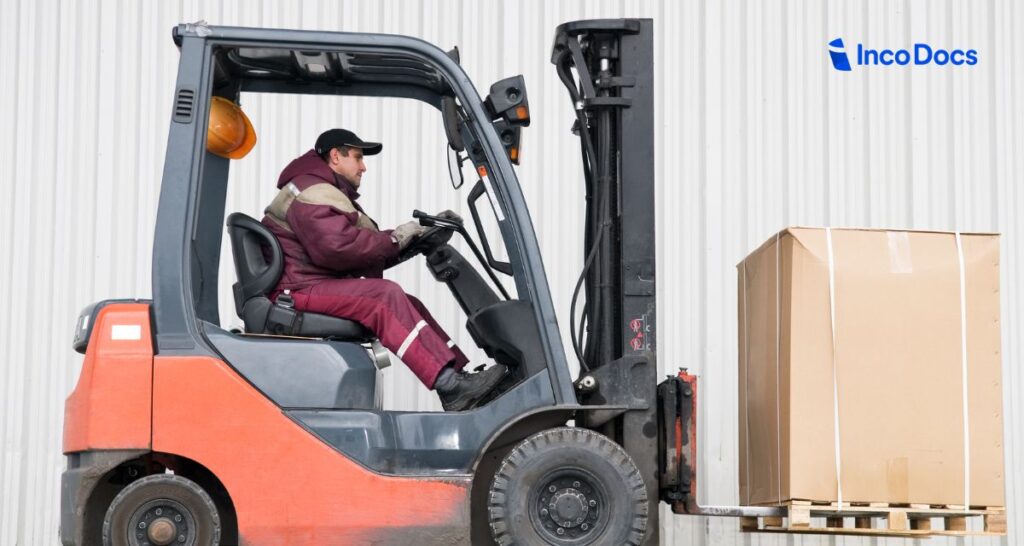
Upon Container Arrival
Once the shipping container arrives, taking a few essential steps ensures the unloading process goes smoothly, while also protecting workers and goods.
Prepare a Safe Working Area
The unloading area must be set up to safely handle incoming containers and all required equipment. There should be enough space for forklifts, pallet jacks, and other machinery to move without obstruction. Ensure the path for the truck is clear of obstacles and vehicles. Sideloaders will need room on the side to lift containers onto the ground safely, while tilt trays require extra space behind the truck to extend the tray and container onto the ground.
Planned routes prevent collisions and keep the workflow smooth. Proper lighting is also needed to spot hazards like broken glass, sharp objects, or leaks. Poor visibility increases the risk of accidents and missed dangers. Place signs and barriers to mark off restricted areas and guide equipment movement. This setup keeps goods and workers safe while minimizing delays and damage.
Confirm that the container sits on stable, level ground. If it’s leaning, use jacks or support blocks to secure its position. A container on uneven ground can cause items inside to shift, making unloading dangerous.
Verify Container Seals and Condition of Goods
Before opening the container doors, check the condition of the container seal and verify the container seal numbers against the shipping documents to confirm no tampering has occurred.
Photograph the container’s exterior, and when the container doors are opened take photos of the goods inside the container. Document everything and if there are any issues you can contact the freight company or supplier to rectify any issues with the container or the products inside.
Safety Gear and Precautions
Workers should wear appropriate Personal Protective Equipment (PPE), such as gloves, steel-toed boots, high-visibility vests and hard hats. Workers should wear appropriate safety gear and personal protective equipment at all times during unloading. Helmets protect against falling objects. Steel-toed boots prevent injuries from heavy items. Gloves help grip and shield hands from sharp edges or rough surfaces.
Inspect for Hazards
Before entering, ensure the area is clear of hazards. Open the doors slowly and from the side to avoid falling cargo. Never stand directly in front of the doors. Inspect for unstable items or any shifts inside. Use barriers or straps to secure loose goods before proceeding further. This prevents sudden shifts that could cause injuries.
Enclosed shipping containers can accumulate fumes, especially if they’ve been sealed for a long time. Open the container doors and allow time for fresh air to circulate once the doors are opened, and consider using fans if necessary to improve ventilation.
Use the Right Tools
Using the right tools and vehicles will ensure the unloading process is easier and more efficient. For example, if the products inside have been packaged onto pallets, using a forklift that has a container loading mast, along with a strong container loading ramp will allow the forklift to drive directly into the container and unload the pallets very quickly. Ensure that drivers are trained and certified, especially if using more specialized equipment. Pallet jacks are an extremely useful tool that can be used to manoeuvre packages around inside the container.
Products can be packaged and loaded inside shipping containers in so many different ways. It’s always a good idea to discuss packaging requirements with the supplier before ordering. Products can be packaged in cardboard boxes, crates, skids, pallets and cases. For example, products that are wrapped and strapped onto pallets will allow the unloading process to be much faster and more efficient, compared to unloading more packages by hand.
Each type of cargo requires a specific approach. Forklifts work well for palletized goods and most medium-sized loads. Conveyor belts can be used for smaller items, reducing manual lifting and streamlining the process. Cranes may be necessary for heavy cargo. For mixed loads, separate heavy items first to avoid shifting that could damage lighter goods. When handling fragile cargo, use manual techniques and soft straps. Avoid stacking and move items slowly to prevent damage. For hazardous cargo, check for leaks and ensure proper ventilation. Use protective gear and keep flammable materials away from heat sources.
Common Container Unloading Challenges and How to Avoid Them
Preventing Cargo Shifts and Spills
Cargo shifts and spills are major safety risks during unloading. When items are not properly secured, they can move unexpectedly. This can cause damage to goods or lead to injuries if items fall. To prevent this, use safety straps and clamps on all loose or heavy items. These tools keep cargo stable and prevent sudden movements when the container doors are opened.
Reinforced supports should be used for bulky or unevenly shaped items. They provide extra stability and prevent items from toppling over. If items are stacked, avoid placing heavier goods on top of lighter ones. Using dividers or braces can help distribute weight evenly and reduce pressure on lower stacks. Always check for any signs of leaning or instability before moving cargo.
Downtime and Labor Costs
Downtime and high labor costs are common challenges that can be managed with proper planning. Efficient labor allocation is the first step. Assign workers based on the type and quantity of goods being unloaded. This reduces the risk of overstaffing and long waiting periods. For large loads, use a smaller team with support from forklifts or conveyor belts. This setup speeds up the process while keeping costs low.
Truck Waiting Time
Truck waiting time is a common issue that raises costs and disrupts schedules. Reducing it starts with effective timing management. Plan truck arrivals and departures to avoid congestion and delays. Use scheduling tools to track trucks and manage dock times. This helps prevent overlapping schedules and keeps operations smooth.
If containers are not unloaded and returned in time, detention fees can quickly add up. To avoid these charges, prioritize unloading based on time limits. Ensure that containers are unloaded and sent back before the deadline. This reduces waiting time and keeps costs under control. Accurate timing is key to minimizing both truck idle time and unexpected fees.
Chemical Safety During Container Unloading
If unloading Dangerous Goods or Hazardous Materials, special care and equipment are needed to ensure safety and prevent contamination. Here’s what is typically required:
- Personal Protective Equipment (PPE)
Workers must wear appropriate PPE based on the type of chemical. This includes chemical-resistant gloves, face shields, respirators, and full-body protective suits. Proper PPE reduces the risk of direct exposure to hazardous substances. - Chemical Spill Kits
Spill kits are essential for containing leaks or spills during unloading. These kits usually include absorbent pads, neutralizing agents, and containment booms. Having spill kits on hand helps quickly manage any chemical leaks, preventing contamination and injuries. - Ventilation and Air Quality Monitors
Chemical fumes can build up inside a container. Use air quality monitors to detect dangerous gas levels. Ventilation systems should be in place to clear the area of any harmful vapors. This step reduces the risk of inhalation and ensures a safe environment. - Explosion-Proof Equipment
For flammable or reactive chemicals, use explosion-proof tools and machinery. This includes forklifts, lighting, and electrical equipment designed to prevent sparks. Standard equipment can pose a fire risk in such environments. - Material Safety Data Sheets (MSDS)
Always have the Material Safety Data Sheets for each chemical on hand. These sheets provide detailed information on handling, storage, and emergency measures. Workers should be familiar with these before unloading starts. - Secondary Containment
Secondary containment areas can be setup around the unloading zone. This prevents leaks or spills from spreading beyond the designated area. Use chemical-resistant mats or dikes to control any overflow. - Emergency Showers and Eye Wash Stations
In case of accidental exposure, emergency showers and eye wash stations should be easily accessible. Workers must know the location and how to use these stations for immediate decontamination.
Read more about Dangerous Goods and IMO Classes, and the difference between Dangerous Goods and Hazardous Materials.
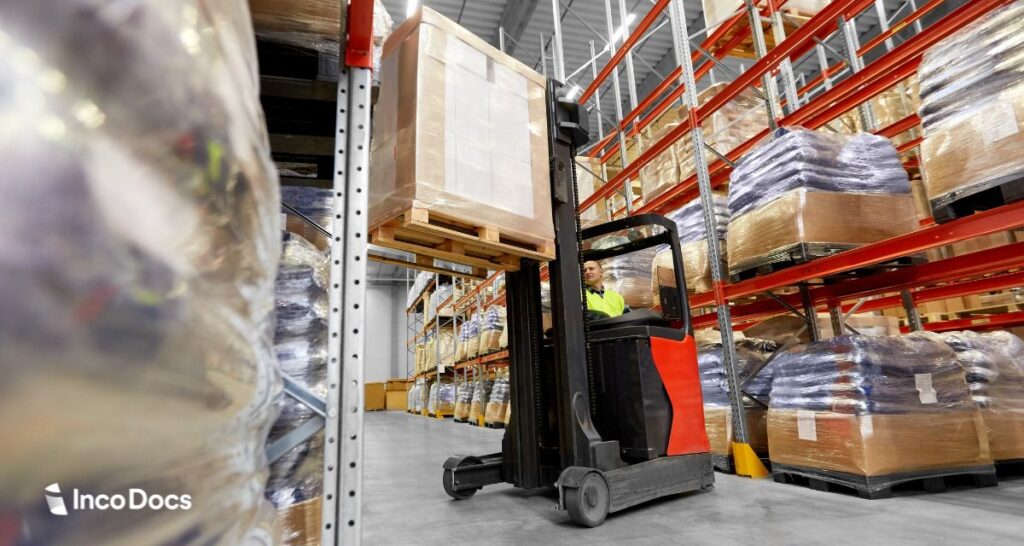
After the Container Has Been Emptied
Once unloading is complete, there are a few final steps to wrap up the process and prevent any additional fees or complications.
Final Safety and Inventory Checks
Inspect the unloading area for any items left behind or damage to the shipping container. Make sure that the container floors are clean and free from any debris. Take photos inside of the empty container and the outside of the container to keep on record. Take a thorough stock count to ensure that you’ve received everything that should have been shipped in the container. You can cross check this from the shipper’s packing list or shipping labels.
Return the Container to the Port
As soon as the container is empty and cleaned, you should contact the freight forwarder or shipping company to come back to collect the empty container. Remember, shipping containers must be returned to the port or nearest depot within a set timeframe to avoid additional detention fees.
Conclusion
Efficient and safe unloading of shipping containers is vital to maintaining a seamless supply chain. By following best practices, from container positioning and selecting the right unloading methods, through to implementing strict safety protocols and using appropriate equipment, businesses can streamline their unloading operations, safeguard workers, and avoid unnecessary costs.
Managing these aspects well also avoids additional container detention fees, ensuring your container operations remain cost effective and on schedule.