Friendshoring, nearshoring, reshoring, and offshoring are supply chain strategies. These help companies decide where to make or source their products.
Two key reasons for change are rising global tensions and the need for stronger supply chains. Geopolitical issues like trade disputes or conflicts, disrupt trade. Many companies now focus on building supply chains that can handle unexpected delays. Other reasons for strategy changes include:
- Geopolitical stability
- Supply chain resilience
- Evolving trade deals
- Lower transportation costs and time
- Shared values and standards
- Consumer preferences
- Reducing risks
This article looks at the benefits and risks of each strategy. It explains what businesses should consider when planning their supply chain.
Key Takeaways
- Friendshoring builds stable supply chains with trusted allies.
- Nearshoring reduces shipping times by moving operations closer.
- Reshoring improves control but comes with higher costs.
- Offshoring saves money but lowers supply chain visibility.
- Each strategy has unique benefits and risks.
- The right choice depends on company goals and market needs.
What is Friendshoring?
Friendshoring is a supply chain strategy where businesses source or produce goods in countries with shared values. These values can include political stability, economic practices, and cultural standards. The goal is to work with trusted allies instead of risky partners.
This idea has grown as businesses face global challenges. Trade disputes and political tensions have caused supply chain disruptions. Friendshoring helps businesses avoid these risks by building safer and more predictable logistics and partnerships.
Unlike offshoring, friendshoring is not just about saving money. It focuses on shared values like fair labor practices and protecting intellectual property. These standards make trading easier and reduce risks for businesses.
Friendshoring also encourages teamwork to solve global problems. Trusted partners can work together on issues like climate change or cybersecurity. While it does not replace other forms of trade, it adds extra security to supply chains.
Benefits of Friendshoring
Friendshoring brings many benefits. It focuses on building supply chains with trusted allies. Here are some key advantages:
- Stronger Relationships: Working with allies can improve political and economic ties. It also allows countries to collaborate on big issues like technology and global challenges.
- Reliable Supply Chains: Friendshoring mitigates the risk of delays caused by conflicts or trade wars. It creates a more stable system.
- Simple Rules: Countries with shared standards make it easier to follow rules. This means fewer problems with regulations and less paperwork.
- Faster Trade: Good relationships lead to smoother negotiations and trade agreements. This helps speed up customs and deliveries.
- Aligned Values: Friendshoring connects businesses to markets with similar values.
Risks of Friendshoring
Friendshoring also comes with risks. Businesses should carefully consider the following challenges:
- Overreliance on Specific Countries: Trading with only a few allies can create dependency. If these countries face problems, supply chains may break.
- Higher Costs: Using ally nations as suppliers can be expensive. These countries often have higher wages and strict rules, which increase costs.
- Trade Tensions: Focusing on allies may upset other nations. This can lead to conflicts or new trade barriers.
- Reduced Flexibility: A small supplier network can limit options. It makes it harder to adapt to market changes or supply issues.
These risks show why balance is important. Mixing friendshoring with other methods can help businesses stay flexible, lower costs, and handle changes better.
What is an Example of Friendshoring?
Friendshoring can be seen in the partnership between the United States and the European Union to boost semiconductor production. A global chip shortage showed weaknesses in supply chains. This pushed both the US and EU to work together in this critical industry.
The goal was to reduce reliance on Asian countries that lead in semiconductor manufacturing. Both the US and EU wanted stronger supply chains and more control over essential technologies.
In 2021 the US and EU announced major investments in domestic chip production. In 2022 the US passed the CHIPS and Science Act. This act set aside billions for manufacturing and research in the semiconductor sector. The EU launched its European Chips Act as part of its Digital Compass plan. It aims to double Europe’s share of global chip production by 2030.
This example shows how friendshoring strengthens supply chains. It focuses on building trust and shared strategic goals between allied nations.
Is Friendshoring a good idea?
Friendshoring is not always the best solution. Some industries, like automotive or electronics, need suppliers with specialized skills. Allied nations may not have what they need. Relying only on friendly countries can slow innovation. It can also make it harder to adapt to changes in the market. Businesses must decide if friendshoring fits their needs before making big decisions.
What is Nearshoring?
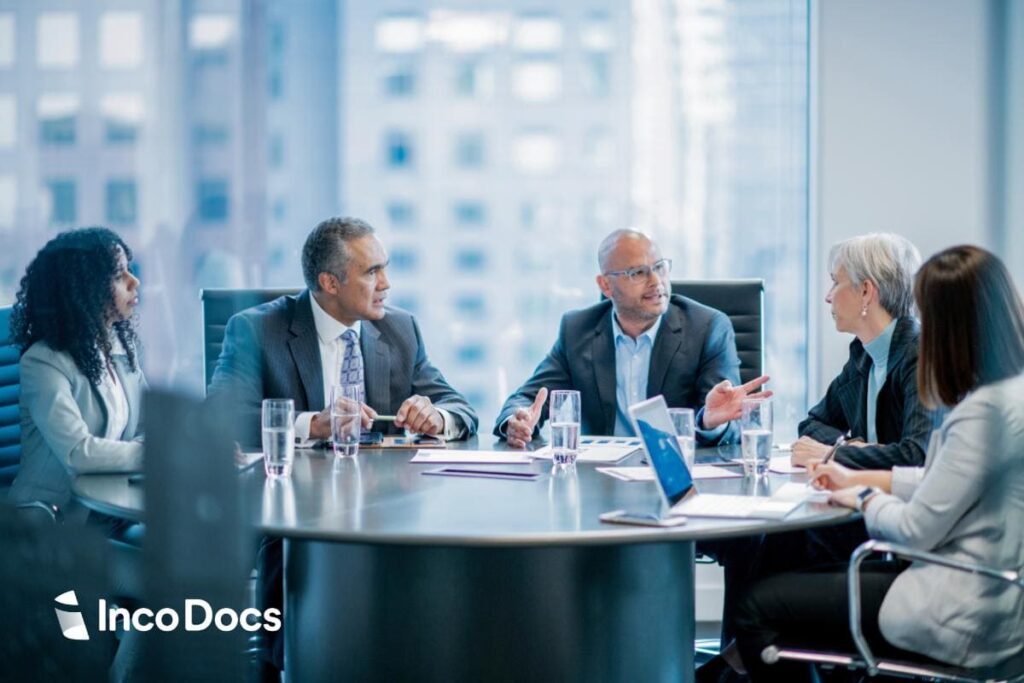
Nearshoring is the approach used when businesses move their operations to suppliers in neighboring or Nearshoring is when a company shifts its supply chain or production to a nearby country. This means working with suppliers that are geographically close rather than in distant locations.
The goal of nearshoring is to reduce shipping time and costs while improving supply chain efficiency. It helps businesses stay flexible and react quickly to changes. Working with nearby suppliers also gives companies more control than offshoring.
This approach saves money without the delays or communication problems of suppliers located far away.
Benefits of Nearshoring
Nearshoring helps businesses cut costs and improve efficiency. Working with nearby suppliers reduces shipping time and makes supply chains easier to manage.
- Lower Costs: Shipping over shorter distances is cheaper.
- Faster Deliveries: Goods arrive quicker with less time in transit.
- Better Communication: Nearby suppliers are easier to reach, with fewer time zone problems.
- Stronger Supply Chains: Spreading production across close countries reduces risks.
- Quick Adaptation: Companies can respond faster to market changes
Risks of Nearshoring
Nearshoring has challenges to consider. Political problems in nearby countries can disrupt trade. This may lead to higher costs or delays.
- Political Instability: Trade policies may change if a partner country faces political issues.
- Economic Risks: Changes in a partner country’s economy can affect costs. Wages or currency values might rise unexpectedly.
- Weak Infrastructure: Some countries lack strong transport systems. Poor roads or ports can slow deliveries.
- Cultural Differences: Neighboring countries may work differently. This can lead to delays or misunderstandings.
What is an example of Nearshoring?
Ford Motor Company is a strong example of nearshoring. The company operates manufacturing plants in Mexico to take advantage of lower labor costs. Ford benefits from nearshoring under the USMCA trade agreement. This allows them to produce vehicles in Mexico at lower costs. It also streamlines cross-border trade with the US.
The close proximity between Mexico and the US helps Ford simplify its supply chain. Parts and finished vehicles can be transported quickly and efficiently across the border. This strategy reduces costs, minimizes delays, and allows Ford to adapt to changes in demand.
What is Reshoring?
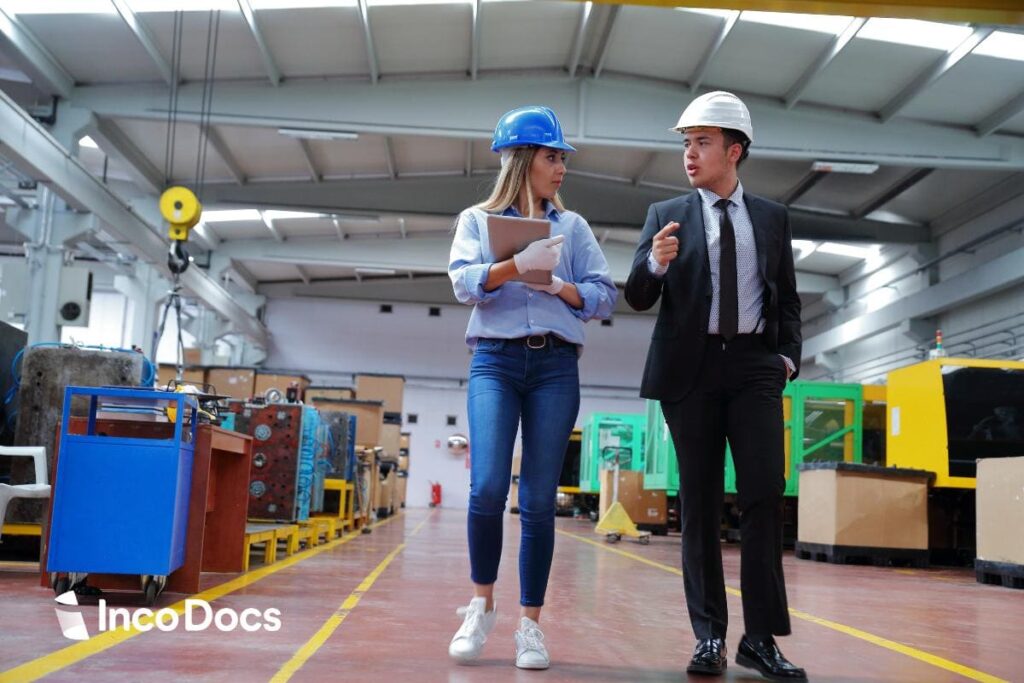
Reshoring is the process of bringing back manufacturing and production activities to a company’s home Reshoring is when businesses relocate manufacturing back to their home country. It means moving production from overseas back under local control.
Businesses choose reshoring to improve quality and control. It helps avoid delays and risks from foreign operations. Companies can also respond faster to customer needs.
Offshoring is the opposite of reshoring. Offshoring sends production abroad to cut costs. Reshoring brings it back to focus on reliability and market demands.
Benefits of Reshoring
Reshoring often moves production closer to the consumer market. This saves time and lowers shipping costs. Shorter supply chains also mean fewer delays and faster deliveries. The benefits of reshoring are:
- Fewer Risks: Companies rely less on unstable global suppliers. This avoids problems like trade disputes or political issues.
- Better Control: Local production gives businesses more control. It is easier to fix problems and adapt to changes.
- More Jobs: Reshoring creates jobs and supports local communities. It also improves a company’s image.
- Faster Shipping: Short distances mean quicker deliveries. Businesses can meet customer needs more easily.
Risks of Reshoring
Reshoring comes with challenges that businesses need to consider. These include higher costs, time-consuming transitions, and regulatory hurdles.
- Higher Costs: Labor and production costs in the home country are often much higher than in offshore locations.
- Supply Chain Issues: Reshoring requires building local supplier networks. This can take time and may increase costs if certain materials are hard to source locally.
- High Setup Costs: Setting up new facilities and training workers can require a big upfront investment.
- Disruptions During Transition: Moving operations back home can cause delays in production and supply. This adjustment period may affect product availability.
- Regulatory Challenges: Companies must comply with strict labor laws and environmental regulations at home. These can add complexity and increase operating costs.
What is an example of reshoring?
A well-known example of reshoring is Stanley Black & Decker’s decision to bring manufacturing back to the US in 2017, the company announced plans for a $35 million factory in Fort Worth, Texas. This move aimed to strengthen their production in the US and improve supply chain efficiency.
Stanley Black & Decker wanted to be closer to their main market. They also hoped to respond faster to customer needs and improve product quality. The “Made in the USA” branding was another key factor in their decision. This label appeals to many American consumers.
Despite its promise, the project faced major challenges. The COVID-19 pandemic disrupted operations and delayed equipment testing. Advanced automation, a key part of the factory, didn’t perform as expected. These issues led to the factory’s closure in March 2023. (source: scmr.com – When Reshoring Projects Fail)
What is Offshoring?
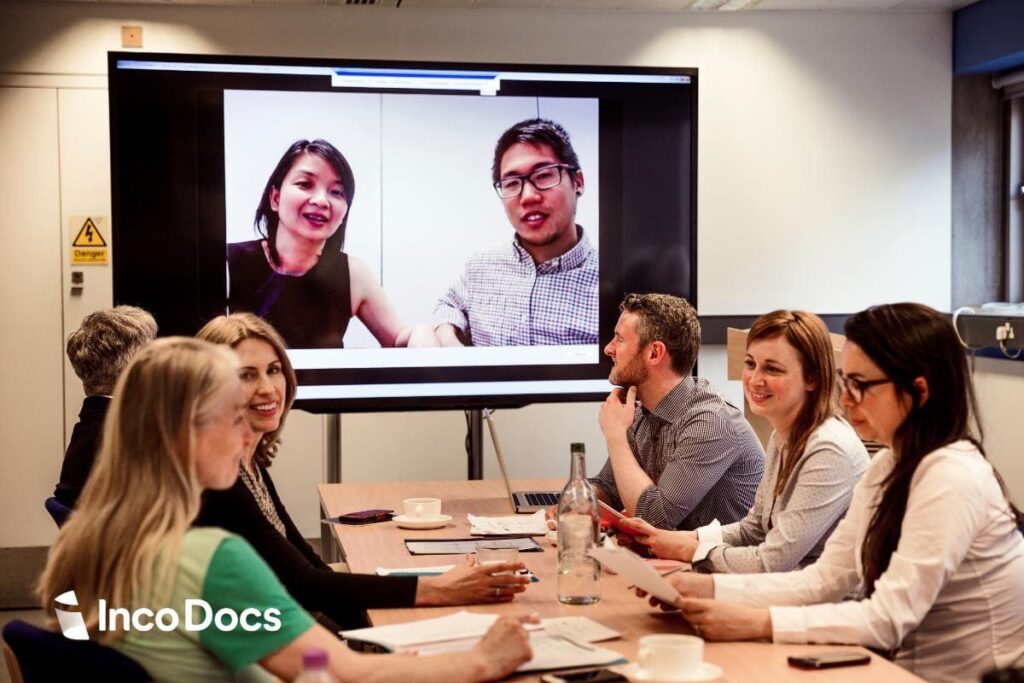
Offshoring is when a company outsources work to another country. This could involves tasks like manufacturing, customer service, or admin work. The goal is to save money by using lower-cost labor.
It helps businesses reduce expenses and stay efficient. By moving some tasks overseas, they can focus on more important goals.
Benefits of Offshoring
Offshoring helps businesses reduce costs and grow faster. It allows companies to access skills and resources that may not be available locally.
- Lower Costs: Hiring workers in some countries costs less. This helps businesses save money on production.
- Skilled Workers: Offshoring allows businesses to find experts in specific areas. These skills can improve products and bring new ideas.
- Faster Operations: Time zone differences allow work to continue 24/7. This speeds up projects and improves customer service.
Risks of Offshoring
Offshoring can help businesses, but it comes with challenges. These risks can slow things down and create problems for companies.
- Political Risks: Relying on foreign suppliers can be risky. Trade disputes or political issues can disrupt operations.
- Longer Shipping Times: Factories far from customers mean slower deliveries. This makes it harder to react to market changes.
- Less Control: Managing production overseas reduces control. Fixing problems or adapting quickly becomes harder.
- Fewer Local Jobs: Moving work abroad can hurt the local economy by reducing jobs at home.
- Language Barriers: Different languages can cause misunderstandings. This slows communication and creates delays.
- Time Zone Delays: Working in different time zones makes decisions slower. Important updates can take longer to share.
Example of Offshoring
A well-known example of offshoring is Apple. Apple designs its products in the United States. However, most of the manufacturing and assembly happens in China. Companies like Foxconn handle this work for Apple. Foxconn is one of the largest electronics manufacturers in the world.
This strategy helps Apple take advantage of lower labor costs in China. It also benefits from China’s strong supply chain systems. These are important for producing electronics on a large scale.
Offshoring allows Apple to keep prices competitive while meeting high demand for its products worldwide. This approach shows how global trade connects economies and relies on partnerships to stay competitive.
What is the difference between offshoring and nearshoring?
The main difference between offshoring and nearshoring is location. Offshoring means moving work to countries far away. Nearshoring means moving work to nearby countries.
Offshoring is often about saving money. Companies choose countries with lower labor costs. But the distance can create challenges. Time zones and cultural differences can make communication harder.
Nearshoring keeps operations closer to home. This reduces shipping times and makes communication easier. It offers some of the cost savings of offshoring but with fewer risks.
The choice depends on what a company values most. Offshoring works for cutting costs. Nearshoring is better for staying flexible and responding quickly to changes.
To Summarize
Managing supply chains is not easy. Companies face many challenges when trying to reduce risks, save costs, and stay profitable.
Friendshoring, nearshoring, reshoring, and offshoring are key strategies. Each has its own benefits and drawbacks. The right choice depends on the company’s goals, its products, and the markets it serves.
A good supply chain strategy needs balance. It should focus on saving costs and improving efficiency. At the same time, it should ensure stability and meet long-term goals.
By carefully choosing the right approach, businesses can build strong supply chains. This helps them stay competitive in a fast-changing world.