The Import Export Podcast
In 2016 the International Maritime Organization (IMO) enforced strict new SOLAS regulations. Greg from BISON Jacks discusses the options that shippers have to comply with Verified Gross Mass regulations when weighing loaded shipping containers for export.
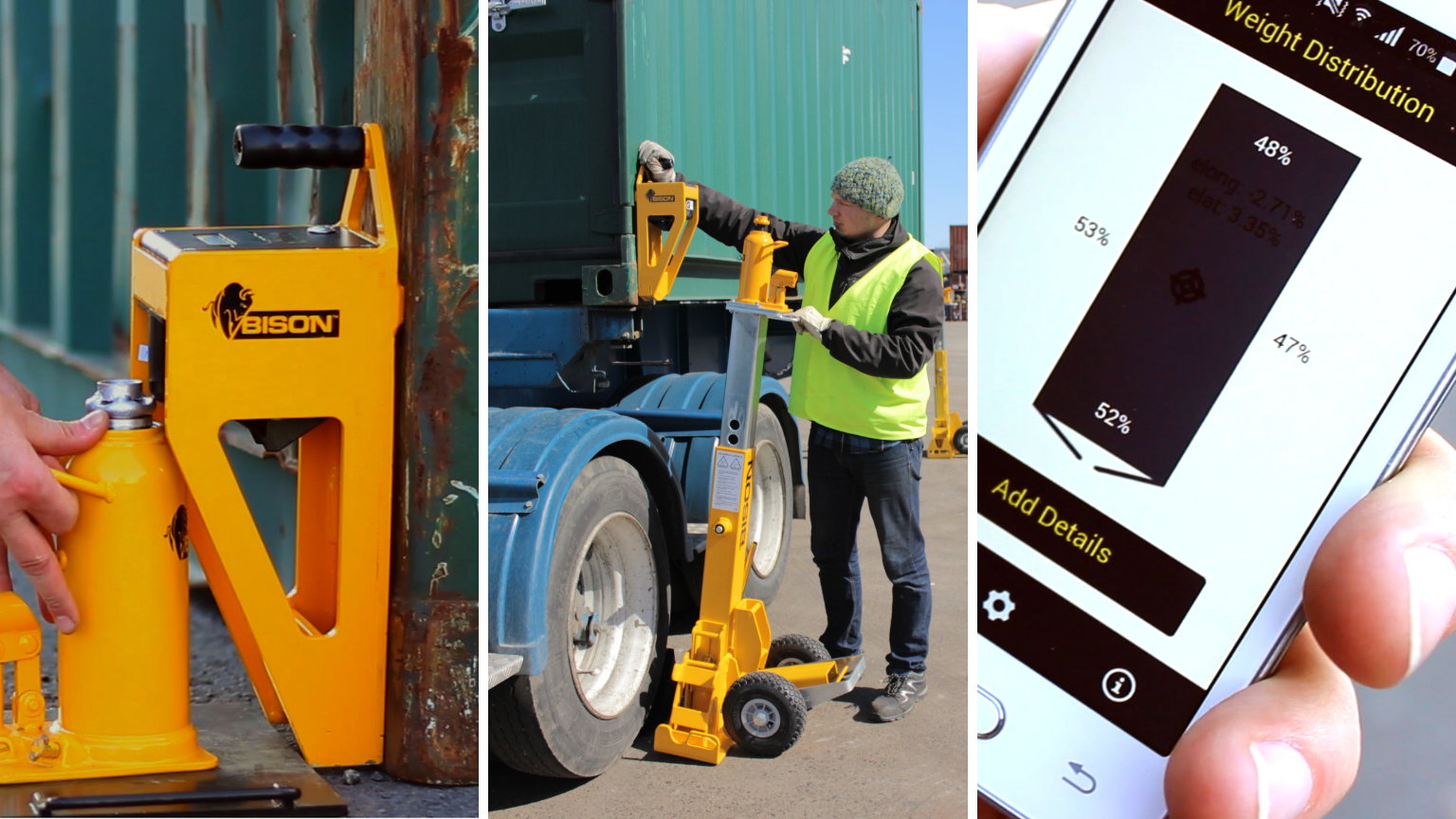
Shippers must use Method 1 or Method 2 to correctly declare gross mass. Greg explains how BISON Jacks came to develop a compact jacks system that allows shippers to weigh loaded shipping containers on site and instantly receive an electronic Verified Gross Mass Certificate. We discuss how this solution can bring time and cost savings in different cases along the supply chain, and how they are used in over 40 countries around the world.
Topics Covered:
- How the new SOLAS regulations in 2016 lead BISON to develop a portable scale for weighing shipping containers
- How the C-Jacks system works, from weighing containers through to receiving an electronic VGM certificate in 5 minutes
- How the system can show a container’s weight distribution, store container photos and historical weight information
- How different companies use C-Jacks to instantly weigh containers to either save time, money or maximize product weight
- How the US Army and companies in over 40 countries use C-Jacks
Listen to Podcast:
Watch Webinar
Are you working on innovative solutions for the Supply Chain? Contact us for Media partnership opportunities.
Contact UsRead full interview here:
Ben: 00:07
Hi, everybody. It’s Ben Thompson here from the Import-Export Podcast. Today we’re talking about SOLAS regulations and some of the options that shippers have to correctly verify the gross mass of their shipping containers and create their VGM declarations.
As most people involved in global trade would be aware, in 2016, the International Maritime Organization introduced strict new SOLAS regulations to ensure that shippers will correctly weigh and verify the gross mass. This is to ensure that containers can be safely loaded and shipped without accidents happening throughout the supply chain.
So, today, we’re joined by Greg, the CEO of BISON Jacks to discuss some options that shippers have to create their VGM declarations. So, Greg, welcome to the show.
Greg: 00:58
Thanks, Ben. Good to be here.
Ben: 01:00
Greg, before we get started, tell me a bit about the experience you’ve had in the logistics industry and how you guys have come about to developing unique solutions for the shipping industry.
Greg: 01:14
Yes. So, I’ve been involved in the container logistics space for the last five to six years mainly as a developer and manufacturer of container lifting and weighing equipment. Back in about 2013, we were a very small company developing a container lift equipment and we had weighing as part of form the control system. And the feedback that we got from the industry then was that the weighing side of it was going to be useful.
People weren’t 100% sure why but it led us to discover that the VGM rule change was on the horizon. And looking a bit further, we saw that there was really no portable system or scales for weighing shipping containers. We saw an opportunity so we conceived a design, filed a patent claim on that, and just started developing a solution that we thought will be useful for shippers once that container weighing requirement came into play.
And as things played out, we were well-positioned in 2016 to support the industry when the alarm bells started ringing around how we’re going to weigh our containers efficiently and satisfy these new weighing rules. So, it’s proven to be a fairly successful product invention build around our container weighing equipment.
Ben: 02:40
Yeah, absolutely. It sounds really good. Obviously, a lot of things have changed and shippers must understand their requirements.
Just as an overview, basically for shippers to comply with the SOLAS regulations, they have two verified ways to weigh their shipping containers. That’s using method 1, which is usually to get the containers weighed at a truck weighbridge on the way to the port and get on charged for those costs. Or they can use method 2which is if they can correctly weigh and verify the weight of their cargo as it’s loaded inside the shipping container, well then they can create their own VGM declaration document.
At IncoDocs, we’ve provided a software tool that allows shippers to create the VGM document, but of course, first, shippers must be able to accurately weigh their cargo before doing so. I understand that your C-Jacks and VGM software is a really unique solution that allows shippers to actually weigh their containers on-site. So, can you tell me a bit about how that process works?
Greg: 03:51
Sure. C-Jacks are method 1 alternative for the VGM. Basically, you can weigh the container physically a number of ways including at a weighbridge or there may be scales attached to the handling equipment somewhere in the chain that can weigh the container.
Our system is a dedicated set of very portable scales that a shipper or a freight forwarder may have in the yard, which they can pullout and use to weigh the container on-site. And the advantage of that is you can weigh the container at the time that’s most convenient time and place for the operation rather than waiting for the container to be weighed, perhaps on roads to the terminal at a weighbridge or at the terminal as well.
When you’re weighing later on in the chain after the containers have been packed and and sealed, you don’t have an opportunity to remedy any issues around the weight for communicating that weight information to the terminal and roads and interested parties.
Basically, to describe the C-Jacks, they’re basically a portable scale attached to the container. There are four scales, actually. They take the bottom corner castings with container, which is hydraulic jacks. You just jack the container clear off the ground or clear of the chassis. And then the load at each corner is sent wirelessly to a smartphone app on a smartphone, and the combined total of those four corners gives you a really accurate gross container weight.
So, the jacks have got a weighing capacity of 35,000 kilograms and you can handle all ISO containers, of all types and sizes, High-Cubes, reefers, flat racks, ISO tanks, basically any container with corner castings. So, suitable for grounded containers. And also, we supply some stands with the kit so that you can weigh containers sitting on chassis as well.
And what’s really cool about it is you get to digitize the weight at the point where you’re weighing the container unlike other scales which tend to produce a little paper docket or just display a number that needs to be written down. With that, an app, which can receive both the weight information from the scales on the spot via Bluetooth, it’ll digitize the weight. It allows you to check the container’s load distribution on the spot.
You can take photos. You can capture other shipment details, perhaps, the CO ID and reference information relating to the container or the shipment. You can then email all of that information will push that out of your app by email to your office or the third parties, and essentially, email a detailed weight record with the VGM certificate attached as soon as the container is weighed.
So, the app keeps information flowing. It can improve efficiency and keep the team in control in critical container information. It’s a lot more efficient than the old pen and paper, calculator method of either calculating the weights underneath it, or getting a weight docket that needs to be taken to the office manually and people manually keying it into a computer system. So, in all of those respects, it’s really compact, efficient, safe tool for taking out to the field, weighing your container and then getting that information straight into the IT system.
Ben: 07:33
Yeah. I’ve seen a video of how it works and I must say it looks very compact, these jacks and quite simple and easy to use. It takes a process that was previously quite complicated and allows somebody to literally weigh a container on-site, to get their weight distribution and VGM declaration and certificate all in one.
How long does it take the process from start to finish for somebody to set up the jacks and weigh a container and get their weight documents? And can anybody do this?
Greg: 08:09
Yeah. It’s really easy to use. The scales have one button. So, very simple for anyone to understand and operate. The time frame is pretty quick. For the containers on the ground, it might take you five minutes for one person to attach the jacks to the container, check it up, weigh the container, seeing that information the way via the app and then pick the system weight.
So, a five-minute operation for a grounded container. Typically, the task is done by the guys or the team responsible for loading the container and they’ll just do that at the end of the process before they close the doors and seal the container. If the container is up on a chassis, the process might take a few minutes longer, maybe eight minutes. It depends a little bit on the sites, the conditions, you’ve got and a few other variables. But it’s a five to eight-minute task depending on the other containers located.
Ben: 09:13
Yeah, sounds good. So, they’re available obviously, for people to weigh containers on-site. How many containers with an exporter have to be shipping for this solution to be workable for their process?
Greg: 09:29
It really depends on the cost of alternative spend, and so the cost of getting your weights wrong. So, I have some examples.
We’ve got a customer in Europe who manufactures furniture. They were paying about 15 Euro per container to have the containers weighed at the terminal for VGM purposes. They shipped 1,300 containers a year. It’s kind of seasonal, it’s not a consistent number every week. But in a corporate year, they were spending nearly 20,000 Euros on terminal weighing charges.
By investing in our equipment, they bought C-Jacks with stands and some back-up equipment as well to ensure that there was no downtime. They got payback of new investment in less than seven months. So, pretty fast. Particularly, in locations where the terminal or the weighbridge charges are quite high, then it’s a really serious option for a shipper and they could save a lot of money by bringing that weighing process in house and avoiding those charges.
Another example would be people who aren’t necessarily looking at it from the point of view of what does it cost me to weigh every container. They could be looking at it from the point of view of what’s the value to us of getting our container weight right..
Ben: 10:58
Absolutely, yeah.
Greg: 11:00
Optimizing the container payload, there’s real value to that, just as people want to maximize the space of the container. Sometimes you might want to maximize the available weight.
Another example would be locals export our seafood and related products. They ship fish oil, which is a really expensive commodity and thousands of dollars per ton. So, optimizing the payload for them is really valuable. They’ve got C-Jacks now, which are portable, they can take it to the different wharves where they’re unloading vessels and piping the fish oil off the vessels directly into the container.
And they can measure the weight of their container in real time and maximize payload. They can stop that, loading it exactly the right point. They can do this rather than disconnecting the container hauling it to a weighbridge, checking it, then come back, reconnect it, keep loading, guess again. It just takes work out of the operations.
So, the shippers of bulk commodities, whether it’s powders, chemicals, liquids, wines, and other example of an industry where we’ve got some really happy customers. The scales are great for just make maximizing payloads.
Ben: 12:23
Yeah, absolutely. There are a few use cases there which I wasn’t really aware of just how important it is to maximize the weight, especially in the case of the fish oil. Otherwise, you’re not just losing time and money. You’re not maximizing the load. You’re not maximizing the sales. So, that’s another great case, yeah.
Greg: 12:46
Yeah. The other scenario we see is people who run the risk of overloading their containers. So, if you’ve got particularly heavy cargo, scrap metal is a good example. If you’re overloaded and get caught, there can be penalties and costs down the shipping and logistics chain. So, if you can weigh that container at the pack point, optimize the load but make sure you’re not overloaded and just eliminate those costs and complications as well.
Ben: 13:19
Yeah, and I think shippers need to take that into consideration, too. It’s not just a cost and time saving but what is the actual cost of getting this wrong. And it can be quite severe if mistakes are made and accidents happen and shippers will be held liable and that can be catastrophic to any business really.
Greg: 13:36
Yeah. The other scenario where the jacks are really useful was the shippers were invoicing customers based on weight as well or volume. And having another certified method of verifying the weight or the volume of the liquid and doing it at source, that can lead to more accurate invoicing, less complications or disputes with counter parties and so on. People trading liquid sand powders and other commodities, they’re using the jacks to just trade with more assurance.
Ben: 14:17
Yeah. That sounds great. And what countries are your jacks available in right now?
Greg: 14:23
Yes. The C-Jacks are in use in about 40 countries now. We’re really proud of that level of uptake around the world. We had quite a lot of sales globally in 2016 as the VGM rule change kicked in, and that’s lead them to be seen quite widely and this leads to continued good business.
So, some of our customers, they include some of the major forwarders, Kuehne + Nagel and DSV. We’ve got BOC Gas, Hexion, GE using them in different parts of the world. BOC Gas is a good example there. In Papua New Guinea, container weighing infrastructure is not readily available. And for them, they’ve got this self-contained system and method of verifying the container weights. We supply calibration kit that allows customers to re-calibrate the scales themselves as well. So, it’s quite self-contained for customers in the islands.
Also in the last year, we’ve got really good orders from military customers. They’re used by NATO in Europe, U.S. Army. A number of bases around the world have adopted them. U.S. Air Force and Navy as well, and a few other defense ministries in Europe as well have made some good orders and deployed them in their operations.
Ben: 15:52
In many places around the world, in many different cases. It’s no doubt they provide a lot of value to people along the supply chain. That’s why you’ve seen so much success. Okay. I think that covers it. As we said, it’s important that shippers understand that these SOLAS regulations are in place and that there are options out there to help them accurately weigh their cargo and quickly weigh their cargo and meet these regulations so that they don’t have any problems or issues along the supply chain.
Your product looks great, congratulations on the progress so far. We’ll keep in touch.
Greg: 16:36
Great. I appreciate it Ben. It’s been really good to talk to you.
Key Takeaways from the SOLAS Verified Gross Mass Regulations Webinar
- Introduction to SOLAS Regulations: In 2016, the International Maritime Organization (IMO) enforced new SOLAS regulations to ensure the correct weighing of shipping containers.
- BISON C-Jacks System: Greg from BISON Jacks introduced a compact jacks system that allows shippers to weigh loaded shipping containers on-site, providing an electronic Verified Gross Mass Certificate.
- Weighing Methods: Shippers can use Method 1 (weighing the container at a truck weighbridge) or Method 2 (weighing the cargo as it’s loaded inside the container) to verify gross mass.
- Digitalization of Weighing: The C-Jacks system digitizes the weight at the point of weighing, allowing for real-time weight distribution checks, capturing container photos, and storing historical weight information.
- Operational Efficiency: The system streamlines the weighing process, taking approximately five minutes for grounded containers and slightly longer for containers on chassis.
- Maximizing Payload: The system is especially beneficial for shippers of bulk commodities, such as fish oil, where maximizing payload is crucial.
- Avoiding Overloading: The system helps prevent overloading, which can lead to penalties and complications in the shipping process.
- Global Availability: BISON C-Jacks are used in over 40 countries, with clients ranging from major forwarders to the U.S. Army.